Excavator Compression
In some cases of soft soil, utilising just the bucket of an excavator pressing and hammering against the vinyl sheet pile is sufficient to drive it to design depth. A steel pile head is typically used to protect the pile top and also distribute the excavator pressing load.
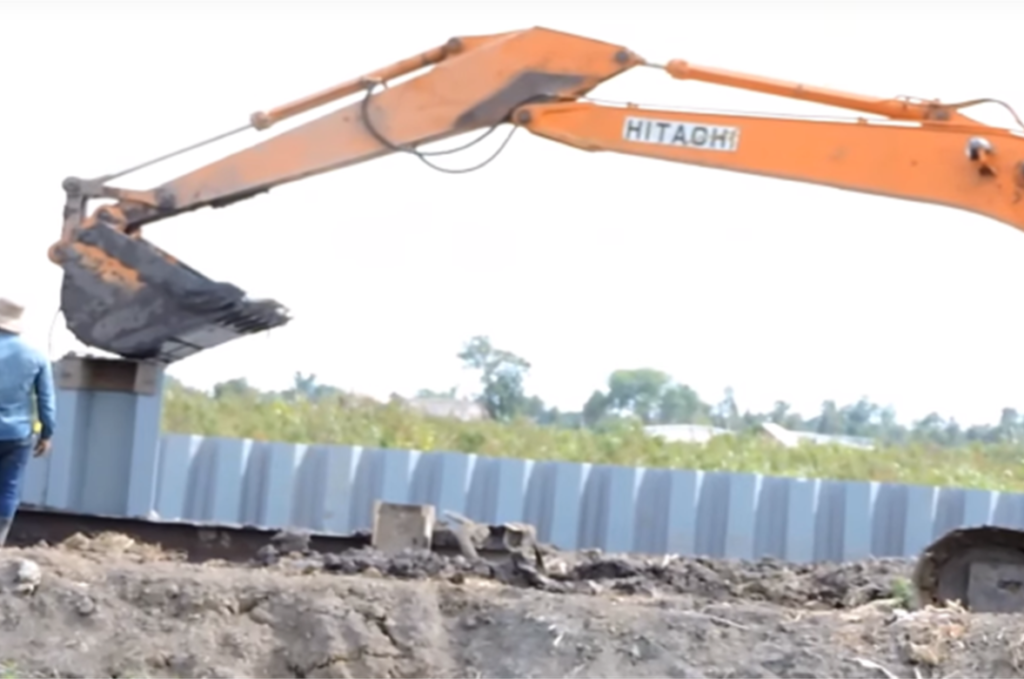
HAMMERING
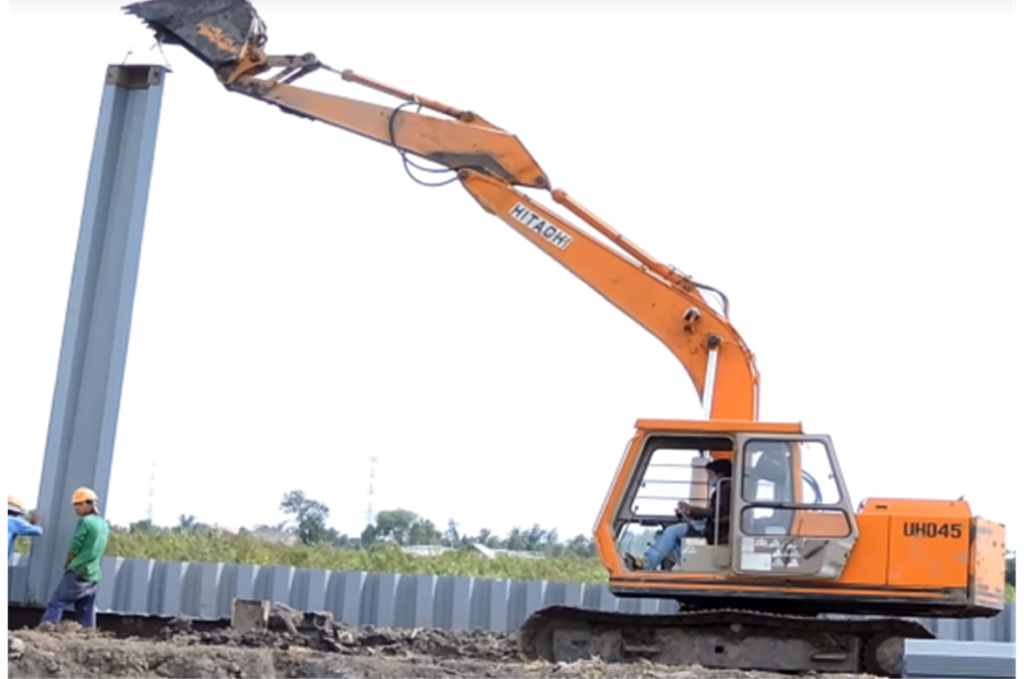
PITCHING
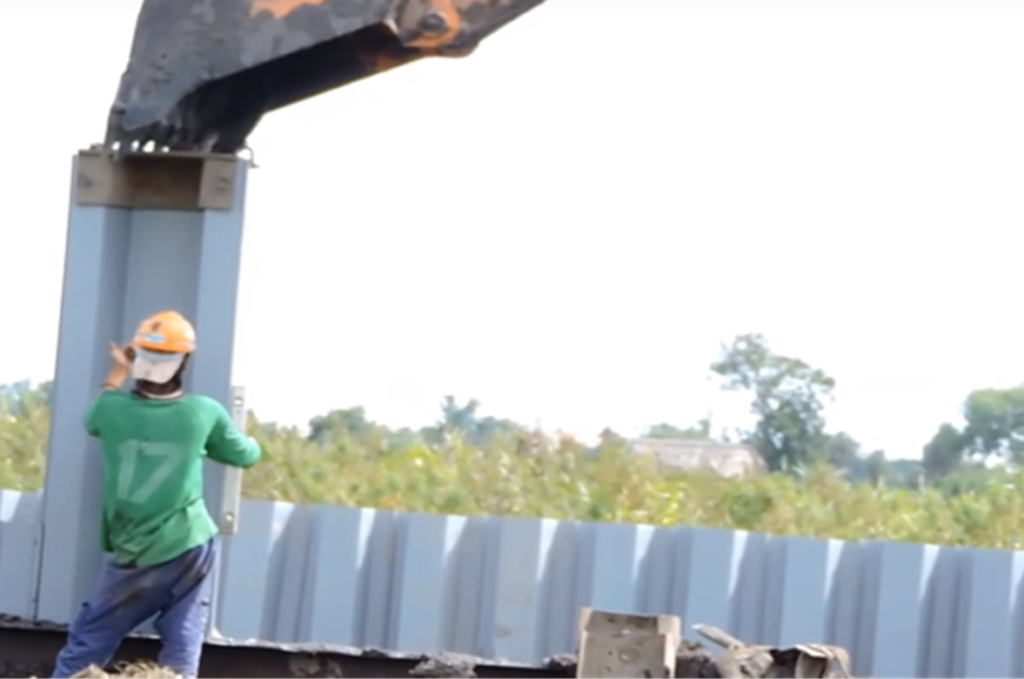
PRESSING
Excavator Mounted Vibrohammer
Suitable vibrohammers for the installation of vinyl sheet piles are typically in the small to medium range. Excavator mounted vibrohammers are an excellent option because of their versatility and the fact that generally the excavator is utilised in other activities prior to and/or after the sheet pile installation such as excavation or soil compaction. The operator has to be mindful of verticality during driving, since unlike the crane, the vibrohammer has to follow the hinge trajectory of the excavator. For tougher soil conditions a mandrel can be used in conjunction with this system—see “Mandrels” section of this installation guide.
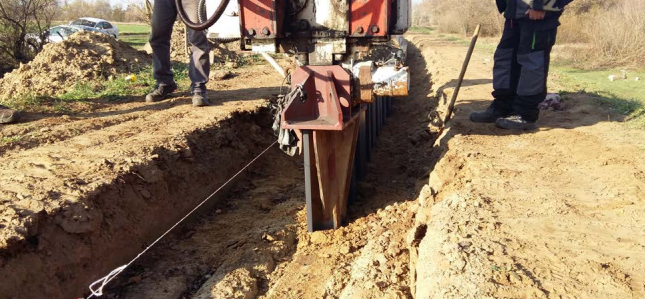
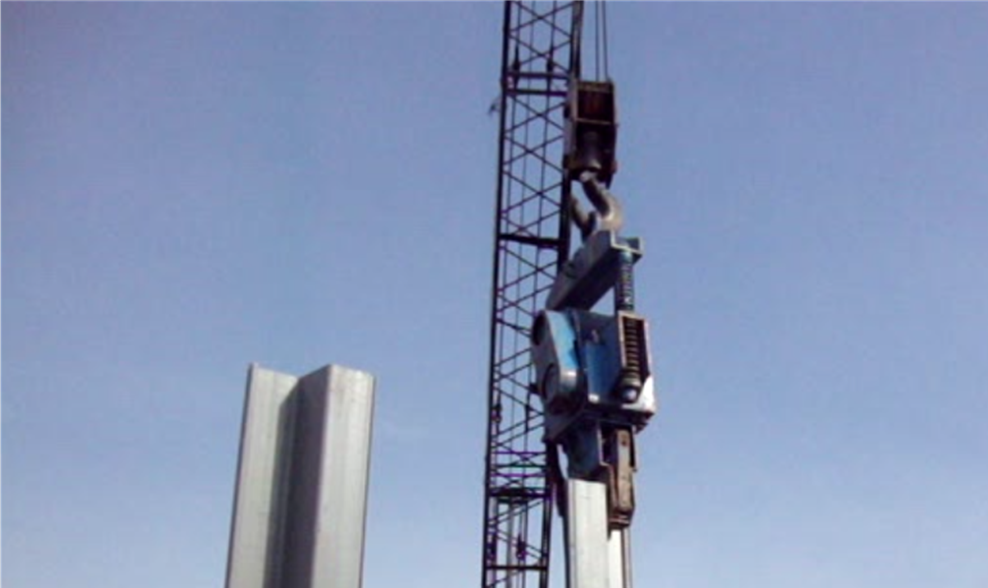
Crane Mounted Vibrohammer
Crane mounted vibrohammer is advantageous over excavator mounted vibrohammer installation as it can effectively handle much longer pile lengths. Also the vibrohammer can effectively rest its weight and force directly on top of the clamped sheet pile which results in better verticality. However, the cost for driving is typically higher than the excavator options due to the extra mobilisation cost of a crane. It must be noted however, that a mandrel is recommended for longer length piles as vinyl sheet piles cannot take the loads that steel can and they could buckle during driving.
DROP HAMMER
A drop hammer is a mechanical simple driving method for driving vinyl sheet piles by lifting and releasing a falling drop hammer weight at low frequency
WATER JETTING
Water jetting may be used in conjunction with other installation methods where the soil is very compacted or cohesive. A high pressure jet of water (or sometimes air) is expelled from the base of the sheet pile loosening the soil as the sheet pile is driven through.
MANUAL INSTALLATION
For extremely soft soils and low driving depths, simple manual tooling can be used to pitch and hammer down the sheet piles with just a few laborers.
Installation Mandrel
A steel sleeve welded to a steel pile head that fits over the Z pile pair or single box pile. The sheet pile is typically horizontally slid onto the sleeve and clamped on by a screw. Then it is lifted over and driven down. Once the design depth is reached or further penetration is refused, the steel mandrel is withdrawn leaving the vinyl sheet pile in place. Equipment Required : Vibrohammer (excavator or crane mounted), Crane or Excavator Suitable for : Slightly more difficult soil conditions where driving the vinyl sheet pile directly is not possible. Also suitable for longer sheet piles with thinner profiles. Advantages : Can penetrate more difficult soils without damaging the vinyl sheet pile.
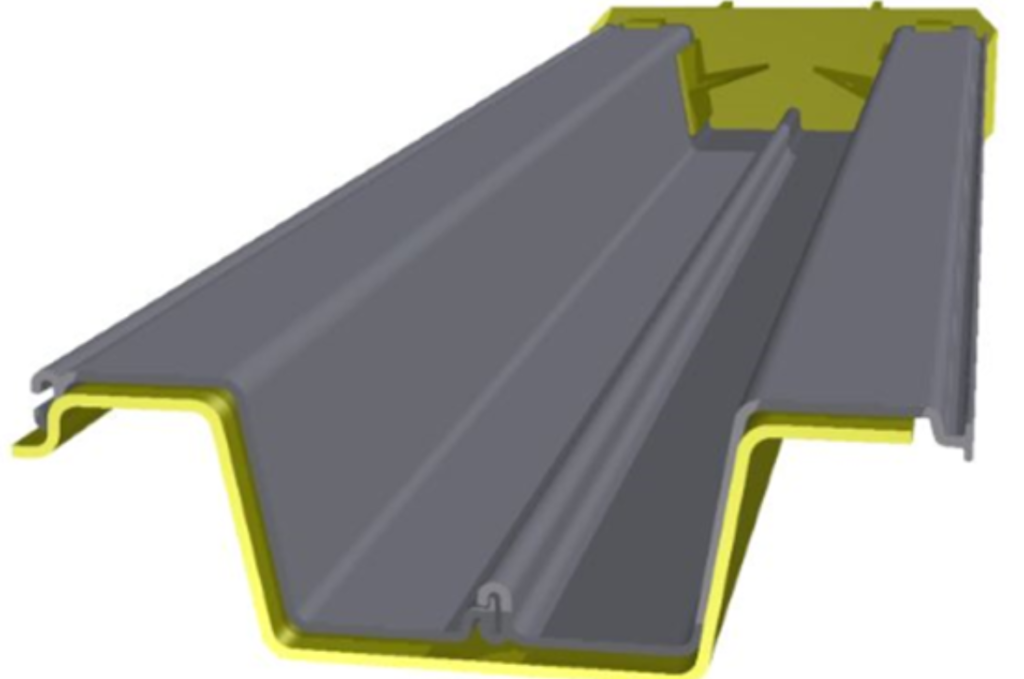
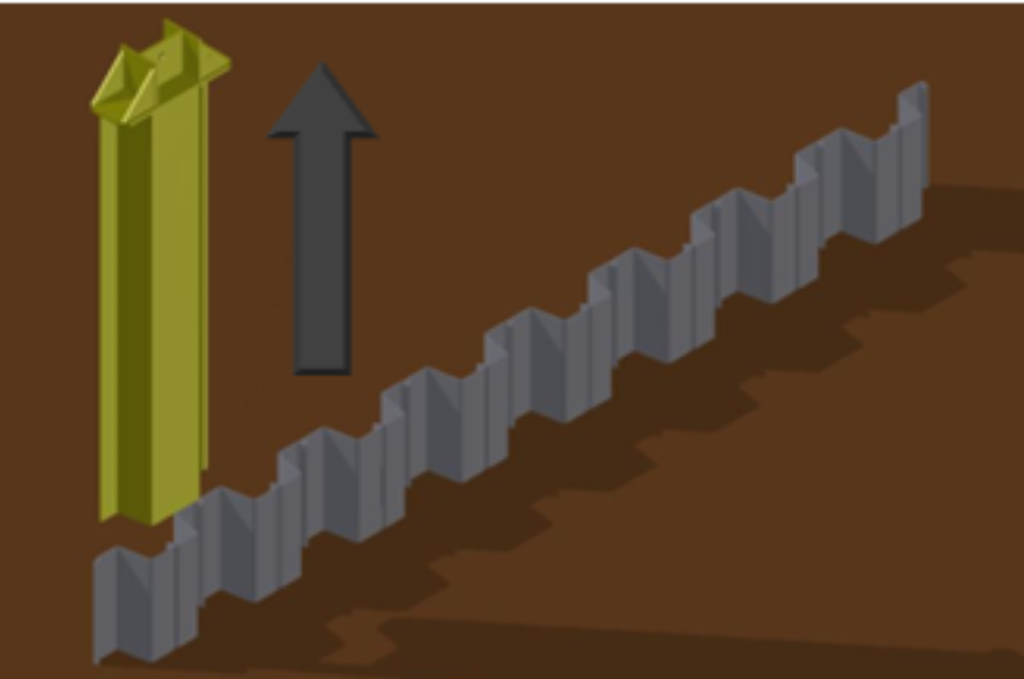
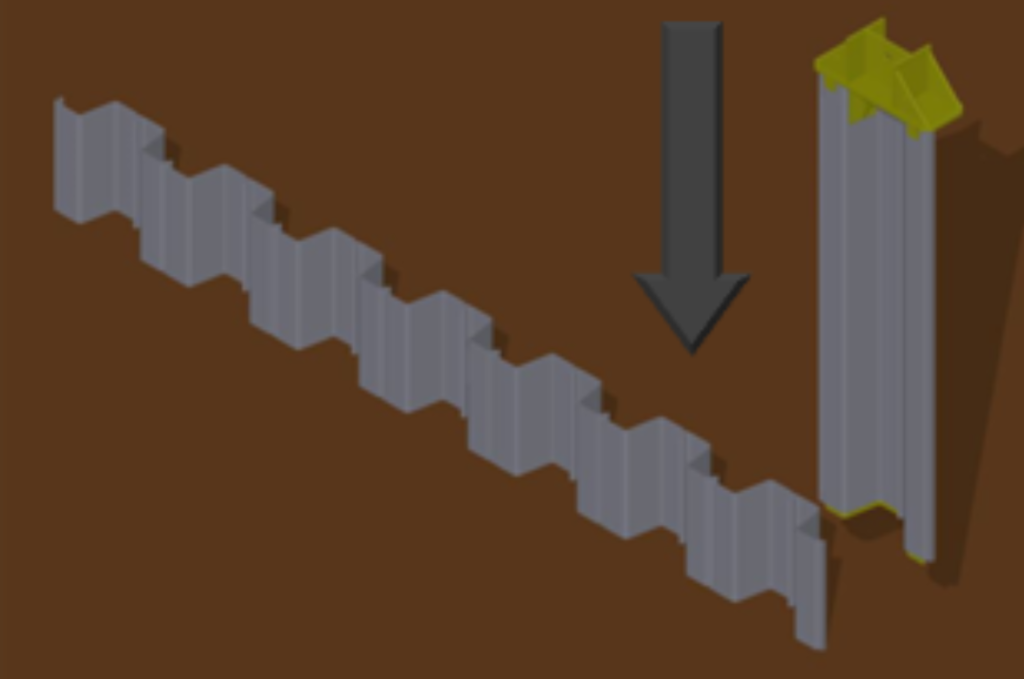
Equipment Required
A drop hammer is a mechanical simple driving method for driving vinyl sheet piles by lifting and releasing a falling drop hammer weight at low frequency
Suitable for
Water jetting may be used in conjunction with other installation methods where the soil is very compacted or cohesive. A high pressure jet of water (or sometimes air) is expelled from the base of the sheet pile loosening the soil as the sheet pile is driven through.
Advantages
For extremely soft soils and low driving depths, simple manual tooling can be used to pitch and hammer down the sheet piles with just a few laborers.
ANCHORING
Vinyl Sheet Piles can be anchored for applications which have a retaining purpose higher than which a cantilevered sheet pile can resist. These are typically anchored via steel threaded bars that can be tensioned against anchor piles or blocks behind the slip plane of the soil. These anchor piles or blocks are typically made of reinforced concrete, PVC or timber. To effectively transmit the dispersed retained load to the anchor rods and pile/block a waling channel on the sheet pile side is used. The design engineer typically specifies in the plan drawings how far back and the size and frequency of these anchors. It is important the installer ensures that there is safe access to the anchor attachments at both ends (and possibly in between if there is a turnbuckle in the middle). ESC also design and supply earth anchors which uses a spade anchor that transfers the tensile forces onto the bearing layer of the soil. It is very important that the tie backs or earth anchors are situated sufficiently far back from the slip plane or active wedge of the soil. This plane is the natural angle the dirt settles too if unsupported and the anchor must be behind that plane.
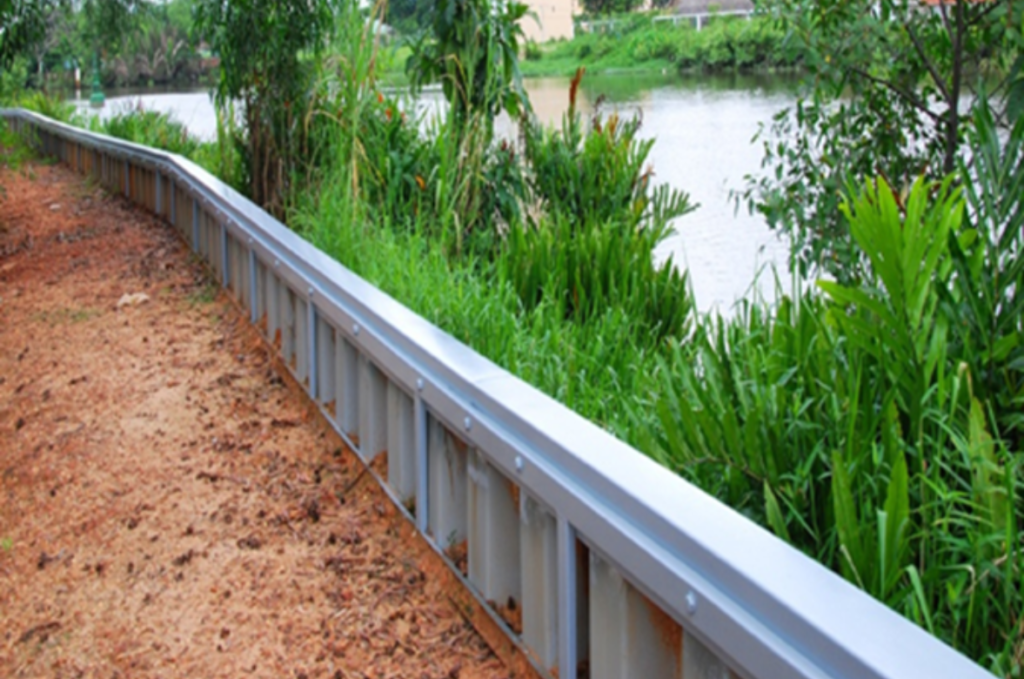
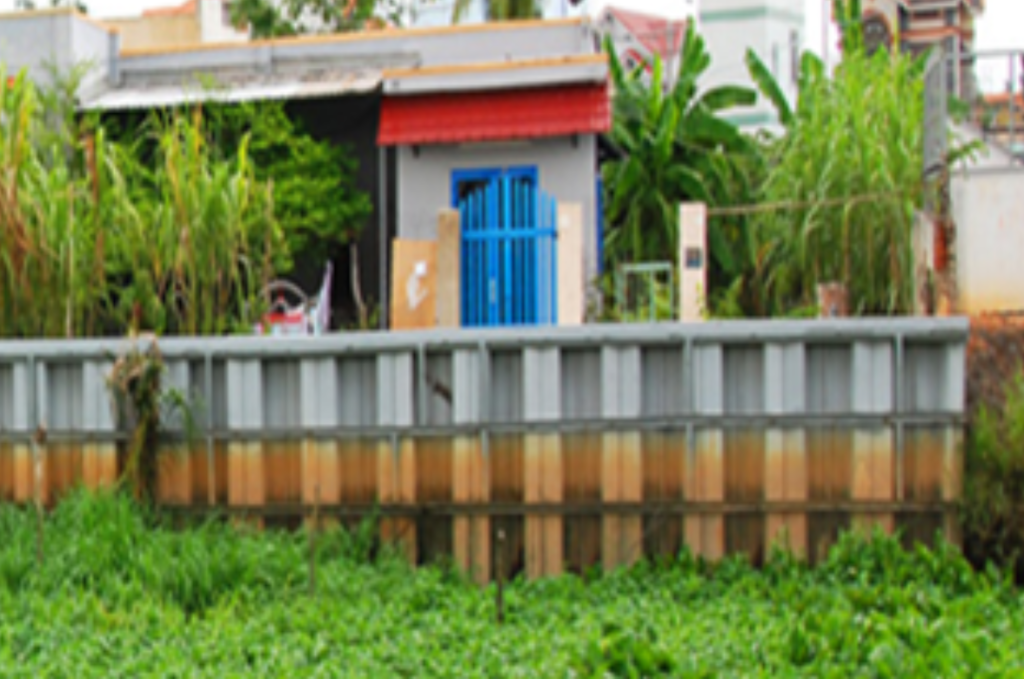
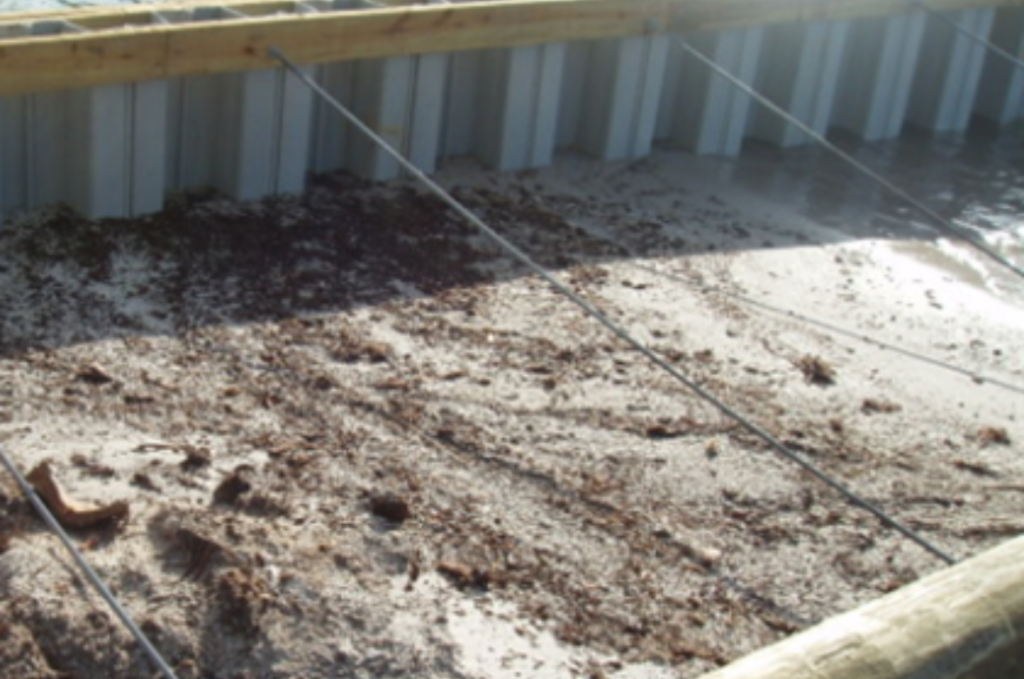